Bamboo: an eco-friendly material for your product
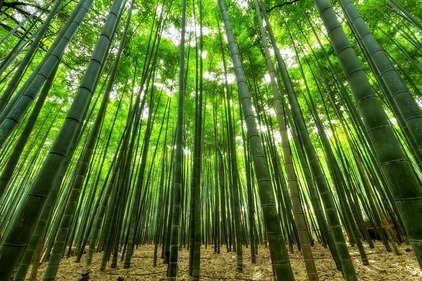
Do you know that September 18 is World Bamboo Day? This is “a day of celebration to increase the awareness of bamboo globally.” [1]
Bamboo is a fast-growing plant and renewable material. Over a thousand species have been discovered worldwide, particularly in the tropical regions of Asia, Latin America and Africa[2]. Within these areas, bamboo has traditionally been used for various purposes as a water transport vehicle, a residence, furniture, an agricultural tool, a fishing tool, food packaging and even for consumption (bamboo shoot). However, many of these untreated bamboo products do not last long due to their short service life (4-7 years)[3]. During the past two decades, bamboo utilisation has been rising because of the increasing interest in the Western European market. However, due to some chemical treatment during its production, there are concerns that bamboo products are not really ‘eco-friendly’. Thus, many research studies attempted to seek clearance on how to extend bamboo’s service life as well as find ways to improve its production processes including material preparation.
Bamboo treatment (material preservation) [4]
This natural material can generally be harmed by fungi, borer and termites; thus, several chemical treatments (e.g. arsenic, boron, copper and chrome), have been introduced as a cheap and effective method for large-scale preservation and extension of bamboo lifespan. Various traditional non-chemical treatments such as lime washing, smoke treatment and water leaching methods have been applied to prevent fungal attacks. Recently, studies have confirmed that these traditional treatments such as the water leaching method can provide decay resistance to bamboo culms almost the same as chemical treatments.
Therefore, sometimes, a right answer for the sustainable resource consumption might already be there, only needing the scientific confirmation.
Bamboo culm
Bamboo culm or stem has regularly been used for construction purposes in local areas; however, its utilisation in Europe has been questioned. To answer this question, a case study in the Netherlands was conducted by Delft University of Technology to investigate the use of bamboo culm as a temporary building material (such as pavilions and tents) [2]. It was discovered that the environmental and financial performance of bamboo is comparable to commonly used material such as Azobe wood, Robinia wood, steel and concrete. Moreover, the result of the environmental assessment showed that the environmental load that was caused from bamboo use in this project was mainly from sea transportation between Costa Rica and the Netherlands. Similarly, another study also highlighted that the utilisation of ‘Plybamboo’ (for flooring or tabletops) in Europe has a higher Eco-cost (due to transport) than local Plywood[5]. Despite the fact that bamboo culm itself is proven to be more eco-friendly than other options, due to transportation burdens it might be better to limit its use in its original land.
Bamboo fibre[6]
Bamboo fibre has become more popular in the textile business since the publication of reports that serviceability and quality (i.e. air-permeable, moisture absorbent, antibacterial and comfy) of bamboo fibres are comparable to cotton. At the same time, regarding sustainability awareness, the issue of the environmentally-unfriendly bamboo fibre production process has also been widely mentioned. This is why many have attempted to find eco-friendlier methods for bamboo fibre production.
Mechanical treatment
This treatment method is the traditional method adopted locally for a long time. Bamboo strips are soaked in water for 3-7 days or boiled (at 90°C) for 10-15 hours. Then, they are crushed, scrapped and combed repeatedly into fibres. However, this method is extremely time-consuming and labour intensive.
Chemical treatment
Chemical treatment is preferable in businesses because this inexpensive method is faster and easier for controlling fibre properties. Although the chemicals are used in fibre treatment only in small amounts, health issues for production workers have been a concern because of corrosive chemicals used during the fibre production process. The often-used compounds are:
- Hydrogen peroxide (H2O2)
- Sodium hydroxide (NaOH)
- Sodium triphosphate (Na5P3O10)
- Sodium sulphate (Na2SO4)
- Sodium carbonate (Na2CO3)
- Sodium hydrogen phosphate (Na2HPO4)
- Sodium silicate (Na2SiO3)
- Sodium citrate (C6H5Na3O7)
Through this chemical treatment, it should be noted that “the important properties of bamboo, such as antibacterial properties, strength, and UV protection, cannot be retained” [6].
Biological/enzymatic treatments
This treatment has been researched and developed to find an eco-friendly method for bamboo fibre extraction. Various enzymes (i.e. cellulase, pectinase, xylanase, and lignin-oxidising enzymes) which are commonly used for other fibres have been studied and tested in the retting process. This eco-friendly treatment is however a very time-consuming process and is not economically feasible.
Combined treatments
A mix of chemical, enzymatic and mechanical processes have been found to be effective in fibre production and more environmentally-friendly than chemical treatment alone.
Bamboo as Bio-material and Biofuel
Apart from the uses above, another group of researchers are currently trying to use bamboo hemicelluloses as (1) bio-material (for applications such tissue engineering, drug delivery and food packaging), and as (2) biofuel and food. However, in order to get economic subsidies and support from governments, extraction processes at industrial scale need to be improved) [7].
To this end, bamboo should be considered as another multifunctional material regarding its numerous advantages. Importantly, the bamboo forest has been reported as another valuable and potential carbon sink for mitigating climate change[8]. Therefore, similar to all other resources, it depends on how much we know about them and how well we manage and preserve them.
References: